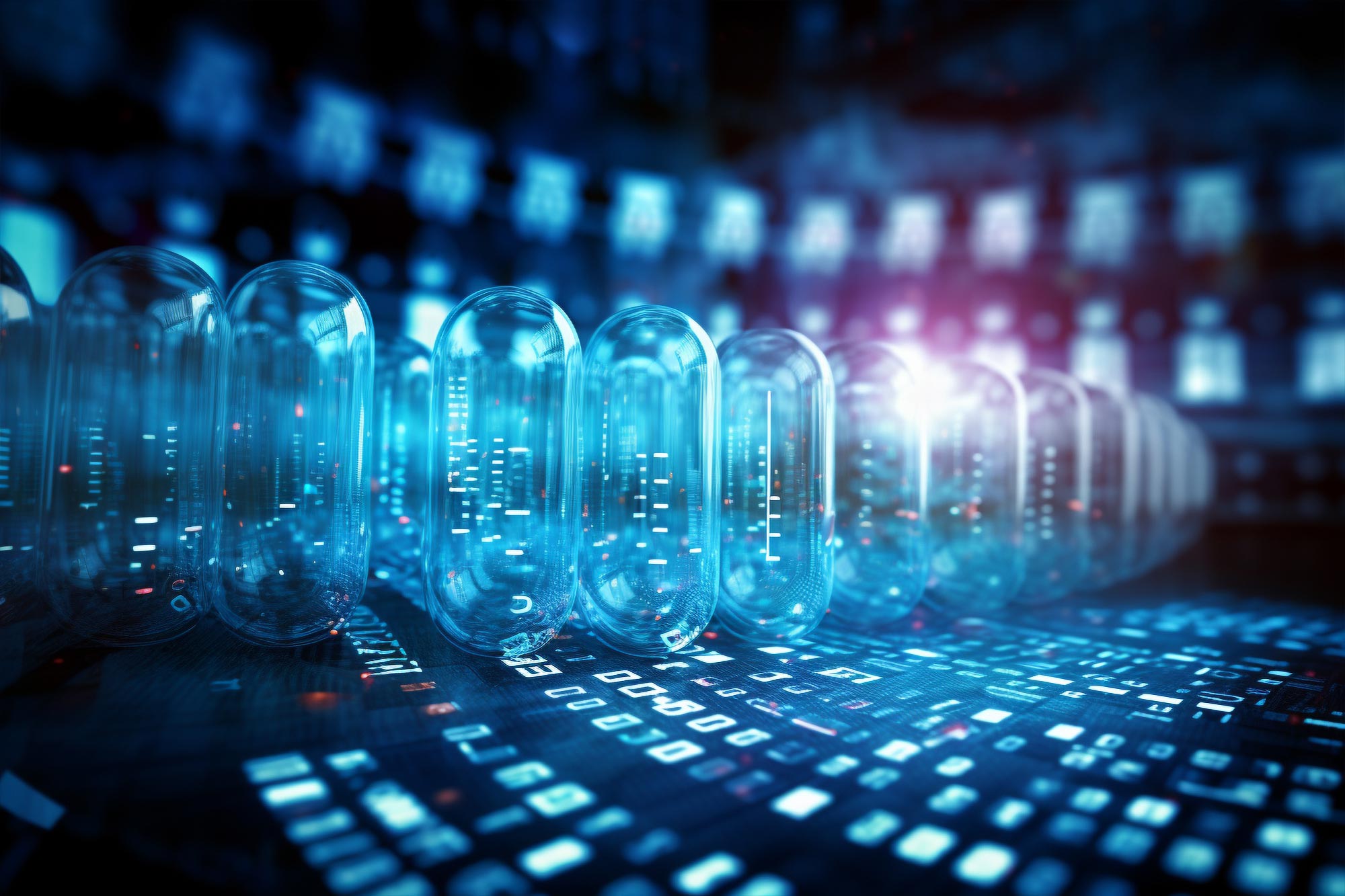
MIT-Takeda Program researchers have developed a physics and machine studying method to boost the manufacturing strategy of pharmaceutical drugs and powders. Their methodology, referred to as PEACE, includes utilizing a laser and machine studying to measure particle measurement distribution, rising effectivity, lowering failed batches, and making the method extra sustainable and cost-effective.
A collaborative analysis crew from the MIT-Takeda Program combined physics and machine learning to characterize rough particle surfaces in pharmaceutical pills and powders.
A team of engineers and researchers from MIT and Takeda are using physics and machine learning to develop improved manufacturing processes for pharmaceutical pills and powders. The aim is to increase efficiency and accuracy, resulting in fewer failed batches of products.
When medical companies manufacture the pills and tablets that treat any number of illnesses, aches, and pains, they need to isolate the active pharmaceutical ingredient from a suspension and dry it. The process requires a human operator to monitor an industrial dryer, agitate the material, and watch for the compound to take on the right qualities for compressing into medicine. The job depends heavily on the operator’s observations.
Methods for making that process less subjective and a lot more efficient are the subject of a recent Nature Communications paper authored by researchers at MIT and Takeda. The paper’s authors devise a way to use physics and machine learning to categorize the rough surfaces that characterize particles in a mixture. The technique, which uses a physics-enhanced autocorrelation-based estimator (PEACE), could change pharmaceutical manufacturing processes for pills and powders, increasing efficiency and accuracy and resulting in fewer failed batches of pharmaceutical products.
“Failed batches or failed steps in the pharmaceutical process are very serious,” says Allan Myerson, a professor of practice in the MIT Department of Chemical Engineering and one of the study’s authors. “Anything that improves the reliability of the pharmaceutical manufacturing, reduces time, and improves compliance is a big deal.”

Real-time measurement of particle size distribution of a pharmaceutical powder using laser speckle imaging and machine learning. Credit: Images courtesy of the researchers
The team’s work is part of an ongoing collaboration between Takeda and MIT, launched in 2020. The MIT-Takeda Program aims to leverage the experience of both MIT and Takeda to solve problems at the intersection of medicine, artificial intelligence, and health care.
In pharmaceutical manufacturing, determining whether a compound is adequately mixed and dried ordinarily requires stopping an industrial-sized dryer and taking samples off the manufacturing line for testing. Researchers at Takeda thought artificial intelligence could improve the task and reduce stoppages that slow down production. Originally the research team planned to use videos to train a computer model to replace a human operator. But determining which videos to use to train the model still proved too subjective. Instead, the MIT-Takeda team decided to illuminate particles with a laser during filtration and drying, and measure particle size distribution using physics and machine learning.
“We just shine a laser beam on top of this drying surface and observe,” says Qihang Zhang, a doctoral student in MIT’s Department of Electrical Engineering and Computer Science and the study’s first author.
A physics-derived equation describes the interplay between the laser and the combination, whereas machine studying characterizes the particle sizes. The method doesn’t require stopping and beginning the method, which suggests the whole job is safer and extra environment friendly than normal working process, based on George Barbastathis, professor of mechanical engineering at MIT and corresponding writer of the research.
The machine studying algorithm additionally doesn’t require many datasets to be taught its job, as a result of the physics permits for fast coaching of the neural community.
“We make the most of the physics to compensate for the shortage of coaching knowledge, in order that we will prepare the neural community in an environment friendly means,” says Zhang. “Solely a tiny quantity of experimental knowledge is sufficient to get consequence.”
At present, the one inline processes used for particle measurements within the pharmaceutical trade are for slurry merchandise, the place crystals float in a liquid. There isn’t any methodology for measuring particles inside a powder throughout mixing. Powders will be constructed from slurries, however when a liquid is filtered and dried its composition adjustments, requiring new measurements. Along with making the method faster and extra environment friendly, utilizing the PEACE mechanism makes the job safer as a result of it requires much less dealing with of probably extremely potent supplies, the authors say.
The ramifications for pharmaceutical manufacturing may very well be important, permitting drug manufacturing to be extra environment friendly, sustainable, and cost-effective, by lowering the variety of experiments corporations have to conduct when making merchandise. Monitoring the traits of a drying combination is a matter the trade has lengthy struggled with, based on Charles Papageorgiou, the director of Takeda’s Course of Chemistry Improvement group and one of many research’s authors.
“It’s a drawback that lots of people try to unravel, and there isn’t sensor on the market,” says Papageorgiou. “It is a fairly large step change, I feel, with respect to with the ability to monitor, in real-time, particle measurement distribution.”
Papageorgiou stated that the mechanism might have functions in different industrial pharmaceutical operations. In some unspecified time in the future, the laser expertise could possibly prepare video imaging, permitting producers to make use of a digicam for evaluation moderately than laser measurements. The corporate is now working to evaluate the instrument on totally different compounds in its lab.
The outcomes come straight from the collaboration between Takeda and three MIT departments: Mechanical Engineering, Chemical Engineering, and Electrical Engineering and Pc Science. During the last three years, researchers at MIT and Takeda have labored collectively on 19 initiatives centered on making use of machine studying and synthetic intelligence to issues within the healthcare and medical trade as a part of the MIT-Takeda Program.
Usually, it might take years for tutorial analysis to translate to industrial processes. However researchers are hopeful that direct collaboration might shorten that timeline. Takeda is a strolling distance away from MIT’s campus, which allowed researchers to arrange exams within the firm’s lab, and real-time suggestions from Takeda helped MIT researchers construction their analysis based mostly on the corporate’s tools and operations.
Combining the experience and mission of each entities helps researchers guarantee their experimental outcomes can have real-world implications. The crew has already filed for 2 patents and has plans to file for a 3rd.
Reference: “Extracting particle measurement distribution from laser speckle with a physics-enhanced autocorrelation-based estimator (PEACE)” by Qihang Zhang, Janaka C. Gamekkanda, Ajinkya Pandit, Wenlong Tang, Charles Papageorgiou, Chris Mitchell, Yihui Yang, Michael Schwaerzler, Tolutola Oyetunde, Richard D. Braatz, Allan S. Myerson and George Barbastathis, 1 March 2023, Nature Communications.
DOI: 10.1038/s41467-023-36816-2