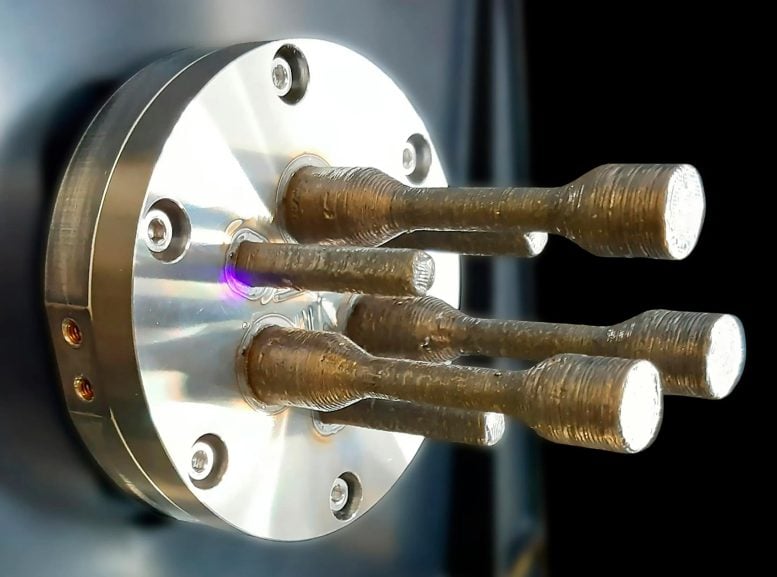
A groundbreaking European-made steel 3D printer has been launched to the Worldwide House Station, marking the primary time steel 3D printing will probably be carried out in orbit. This initiative, which leverages a collaboration between ESA and Airbus, goals to show the potential of in-space manufacturing. Credit score: Airbus Defence and House SAS
Metallic 3D printing will quickly happen in orbit for the primary time. A pioneering European-made steel 3D printer is on its technique to the Worldwide House Station (ISS) on the Cygnus NG-20 resupply mission which launched this week.
“This new 3D printer printing steel components represents a world first, at a time of rising curiosity in in-space manufacturing,” explains ESA technical officer Rob Postema. “Polymer-based 3D printers have already been launched to, and used aboard the ISS, utilizing plastic materials that’s heated on the printer’s head, then deposited to construct up the specified object, one layer at a time.
“Metallic 3D printing represents a higher technical problem, involving a lot greater temperatures and steel being melted utilizing a laser. With this, the protection of the crew and the Station itself must be ensured – whereas upkeep potentialities are additionally very restricted. If profitable although, the energy, conductivity, and rigidity of steel would take the potential of in-space 3D printing to new heights.”
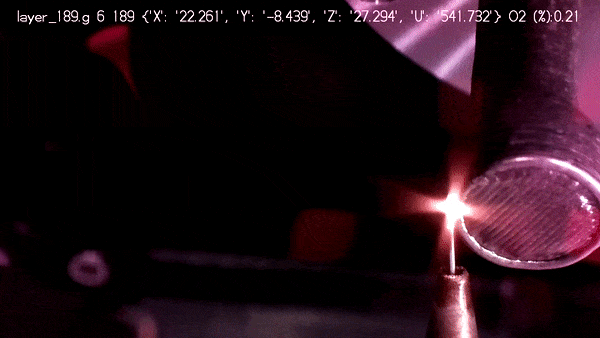
The primary steel 3D printer to function aboard the Worldwide House Station seen throughout floor testing, producing an ESA-design pattern half. Its growth led by ESA, this Metallic 3D Printer goals to show that steel 3D printing could be carried out in weightless circumstances, opening the way in which to a future in-space manufacturing functionality the place astronauts removed from Earth can produce no matter instruments or spare components they want. Credit score: Airbus Defence and House SAS
Printing in House
The Cygnus NG-20 spacecraft, carrying the Metallic 3D Printer together with 8,200 kilos of scientific investigations and cargo, docked to the Worldwide House Station on February 1. As soon as is unpacked, ESA astronaut Andreas Mogensen will put together and set up the roughly 180 kg Metallic 3D printer within the European Draw Rack Mark II in ESA’s Columbus module. After set up, the printer will probably be managed and monitored from Earth, so the printing can happen with out Andreas’s oversight.
The Metallic 3D Printer expertise demonstrator has been developed by an industrial workforce led by Airbus Defence and House SAS – additionally co-funding the challenge – below contract to ESA’s Directorate of Human and Robotic Exploration.
“This in-orbit demonstration is the results of shut collaboration between ESA and Airbus’ small, dynamic workforce of engineers,” feedback Patrick Crescence, challenge supervisor at Airbus. “However this isn’t only a step into the longer term; it’s a leap for innovation in house exploration. It paves the way in which for manufacturing extra advanced metallic constructions in house. That could be a key asset for securing exploration of Moon and Mars.”
The printer will probably be printing utilizing a sort of chrome steel generally utilized in medical implants and water therapy resulting from its good resistance to corrosion.
The stainless steel wire is fed into the printing space, which is heated by a high-power laser, about 1,000,000 occasions time extra highly effective than your common laser pointer. Because the wire dips into the soften pool, the top of the wire melts, and steel is then added to the print.
ESA supplies engineer Advenit Makaya from the ESA’s Directorate of Expertise, Engineering and High quality, supplied technical help to the challenge: “The soften pool of the print course of may be very small, within the order of a millimeter throughout, in order that the liquid steel’s floor stress holds it securely in place in weightlessness. Even so, the melting level of chrome steel is about 1400 °C so the printer operates inside a completely sealed field, stopping extra warmth or fumes from reaching the crew of the House Station. And earlier than the print course of begins the printer’s inner oxygen environment must be vented to house, changed by nitrogen – the recent chrome steel would oxidize if it turned uncovered to the oxygen.”
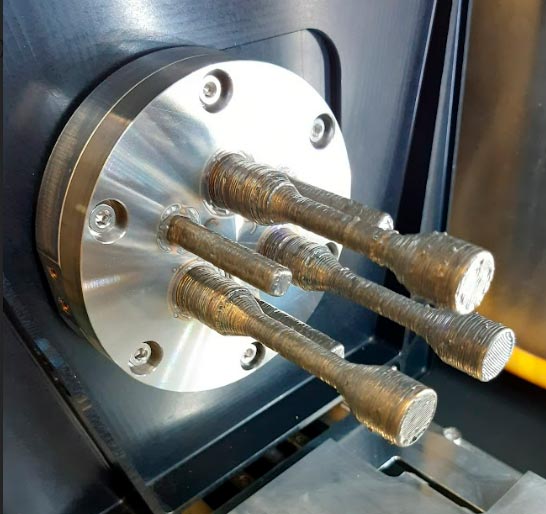
The Metallic 3D printer would be the first time a 3D printer will print in steel on the Worldwide House Station. ESA contracted Airbus Protection and House SAS to provide the 3D printer and it’ll characteristic a stainless-steel wire that will probably be melted utilizing a excessive powered laser and print 4 prints, every taking two to 4 weeks to complete printing.
It was launched on NG-20 on January 30, 2024. Credit score: Airbus Defence and House SAS
Shapes and Sizes
4 fascinating shapes have been chosen to check the efficiency of the Metallic 3D printer. These first objects will probably be in comparison with the identical shapes printed on floor, referred to as reference prints, to see how the house atmosphere impacts the printing course of. The 4 prints are all smaller than a soda can in dimension, weigh lower than 250 g per print, and takes about two to 4 weeks to print. The scheduled print time is proscribed to 4 hours day by day, resulting from noise rules on the House Station – the printer’s followers and motor of the printer are comparatively noisy.
As soon as a form has been printed, Andreas will take away it from the printer and pack it for secure travels again to Earth for processing and evaluation, to grasp the variations in printing high quality and efficiency in house, versus Earth.
One reference and 0xg print, which is part of a devoted software, will go to the European Astronaut Centre (EAC) in Cologne, Germany. One other two will probably be headed to the technical coronary heart of ESA, the European House Analysis and Expertise Centre (ESTEC), the place a workforce on the Supplies and Electrical Elements Laboratory awaits the samples for macro and micro evaluation of the printed components. The ultimate print will go to the Technical College of Denmark (DTU), who proposed its form, and can examine its thermal properties in help of e.g. future antenna alignment.
Getting ready for the Future
“As a expertise demonstration challenge, our goal is to show the potential of steel 3D printing in house,” provides Rob. “We’ve already discovered lots getting so far and hope to be taught much more, on the way in which to creating in-space manufacturing and meeting a sensible proposition.”
One in all ESA’s targets for future growth is to create a round house financial system and recycle supplies in orbit to permit for a greater use of sources. A method can be to repurpose bits from outdated satellites into new instruments or constructions. The 3D printer would get rid of the necessity to ship a software up with a rocket and permit the astronauts to print the wanted components in orbit.
Tommaso Ghidini, Head of the Mechanical Division at ESA, notes: “Metallic 3D in house printing is a promising functionality to help future exploration actions, but additionally past, to contribute to extra sustainable house actions, by means of in-situ manufacturing, restore and maybe recycling of house constructions, for a variety of functions. This consists of in-orbit giant infrastructure manufacturing and meeting in addition to planetary long-term human settlement. These features are key focuses in ESA’s upcoming expertise cross-cutting initiatives.”
Thomas Rohr, overseeing ESA’s Supplies and Processes Part, provides: “This expertise demonstration, showcasing the processing of metallic supplies in microgravity, paves the way in which for future endeavors to fabricate infrastructure past the confines of Earth.”